How recyclable is the Fairphone 2?
From the dawn of the industrial era up to today, the majority of our products have been created according to the principles of a linear economy: we find resources, make a product, and then dispose of it when we’re done using it. But in recent years, there’s been growing awareness of the need to move to a circular economy: a production approach that aims to maximize the usefulness of products, components and materials across the whole lifecycle. In terms of recycling, this means achieving maximum recovery of materials once products reach the end of their usable life.
While circularity is certainly the long-term goal, Fairphone (and the manufacturing industry as a whole) don’t yet have all the necessary capabilities to make it a reality. However, we’re laying the groundwork, one step at a time. To start, we’ve designed the Fairphone 2 to last as long as possible. We’re also tracing where the materials in our phone come from, and working to identify the various issues in each of these supply chains.
Our latest step looks at the end-of-life phase. Eventually, when they are no longer usable or repairable, or reused by somebody else, our phones will make the sad transition from our constant companion to electronic waste. And when that time comes, we want to understand how the Fairphone 2 should be recycled to recover the greatest percentage of materials. Read on for a summary of report findings, or download the full Fairphone Recyclability Report.
How does electronics recycling work?
For a long time, recycling has been viewed as the panacea of sustainability. Once you’re done using something, you recycle it (instead of just throwing it away). All good, right?! But it’s not that simple, of course. Have you ever thought about what happens to products after you put them in the recycling bin? How does recycling actually work?
For products that are made of a single material (like glass), the process can be as simple as melting it down to reusing it. But complex consumer products are much trickier. A United Nations Environment Program (UNEP) report on metal recycling includes a great analogy: Imagine making your morning coffee. With the right tools, it’s easy to combine the water, coffee, milk and sugar to create your drink (similar to a linear economy). But if you had to separate it again into the original four ingredients (as required by a circular economy), that would be rather challenging.
Just like the example above, the objective of recycling consumer electronics is to recover as many of the original materials as possible in a reusable form. This is achieved using a combination of steps including dismantling, size reduction (shredding), physical sorting and further processing.
But what you get out does not equal what you put in. The efficiency of recycling consumer electronics depends on the design of the products, the properties of the materials they are made of, how well the waste is collected and sorted, and the actual recycling processes that are used. Even in the best-case scenario, materials will be lost at every step. In addition, recycling also consumes energy, meaning recovered materials still come at a cost to the environment. You can read extensively about these limitations in the UNEP report referenced before.
Let’s bring in the experts: An analysis using the Recyclability Index
To help us gain a better understanding of the different issues related to electronics recycling, we turned to two very bright minds: Dr. Antoinette van Schaik (MARAS B.V.) and Prof. Dr. Dr. h.c. Markus A. Reuter (Freiberg, Germany), both renowned experts in recycling, sustainable technologies for metallurgy and digitalizing the circular economy. We commissioned them to investigate the recyclability of the Fairphone 2 using the Recyclability Index and Material Flower developed by van Schaik and Reuter.
After the completion of the study, we have identified at least 45 different elements (or materials).
With this study, our aim was to research the potential recovery of all these materials in every part of the phone – from the external housing down to the tiniest capacitor.
Specifically, we wanted to know which currently available recycling methods would most efficiently recover the greatest amount of materials and if modularity can be of any influence in improving recovery.
To find out, van Schaik and Reuter started with the wealth of information from the full material declarations we’ve collected from all the (sub-)suppliers we could reach, and combined it with the powerful HSC Sim 9 metallurgical and physical separation process simulation software from Outotec. The software allowed them to create models of how all the different elements, alloys, plastics and materials associations in the Fairphone 2 behave in the best recycling technologies available today and which existing techniques could offer the highest recovery rates.
The sophisticated models they produced not only show what could be recovered – they also reveal what is lost, and at which stage of the recycling process, because the simulations captured the full composition of scrap particles. For example, some processes cause complete loss of magnesium due to oxidation, while others might cause all the plastics to be used as fuel instead of being recovered.
Note: The figure below shows the simulation and modeling process of the metallurgical processes. We have also investigated shredding and physical sorting. For this and more detail, please read the full Fairphone Recyclability Report.
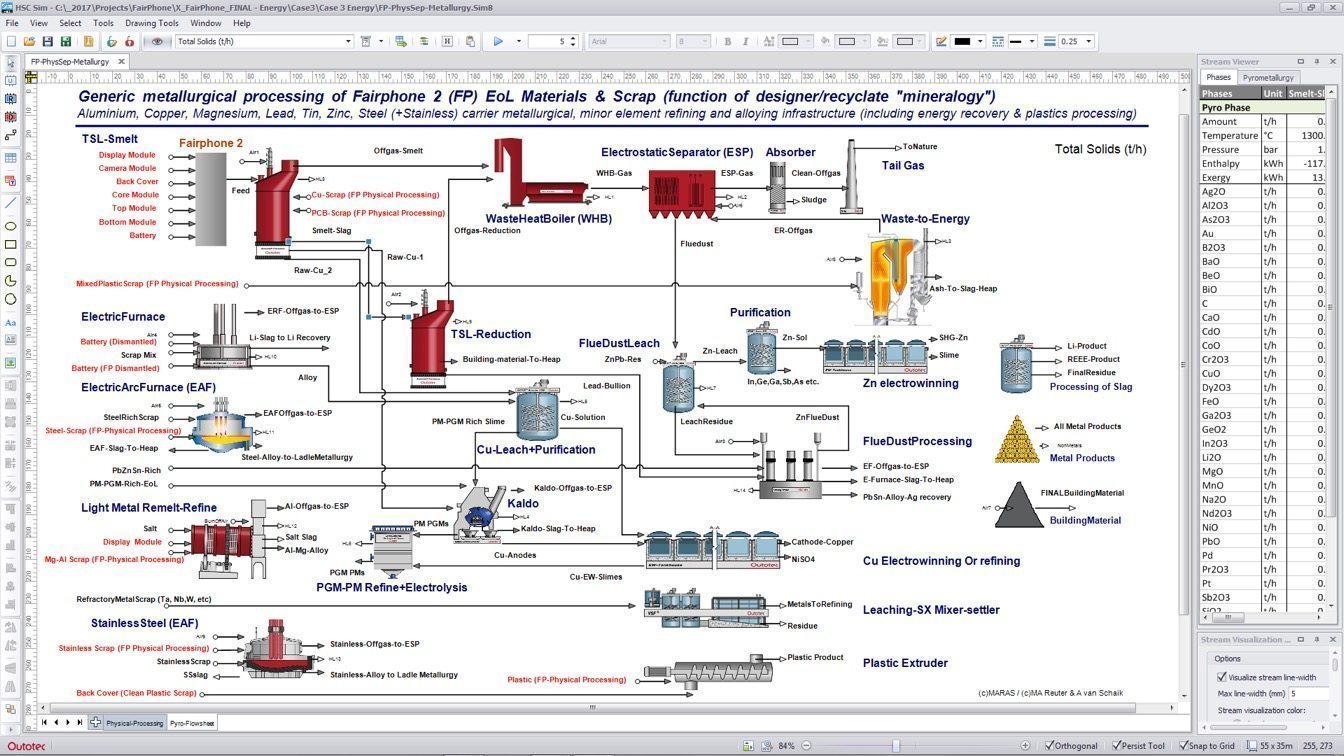
Smelting, dismantling and shredding: Three potential recycling routes
The study identified and analyzed three different recycling routes that could potentially be used for the Fairphone 2. These different routes are based on different combinations of existing best available techniques (BAT) that recycling and processing companies use, but it is good to note that recycling companies are focussed on recovering specific materials and so not all available techniques are always applied under the same roof. The imperative of this study is the most optimized recovery of materials and environmental footprint of BAT processes. This implies the flowsheets are technologically and economically viable, but these may differ considering the business objectives of the recycling companies.
Route 1: Smelting
Total smelting: Feeding whole Fairphones into a high-temperature metallurgical furnace, recovering the materials mainly as metals, alloys and inorganic compounds while also using embodied energy of plastics.
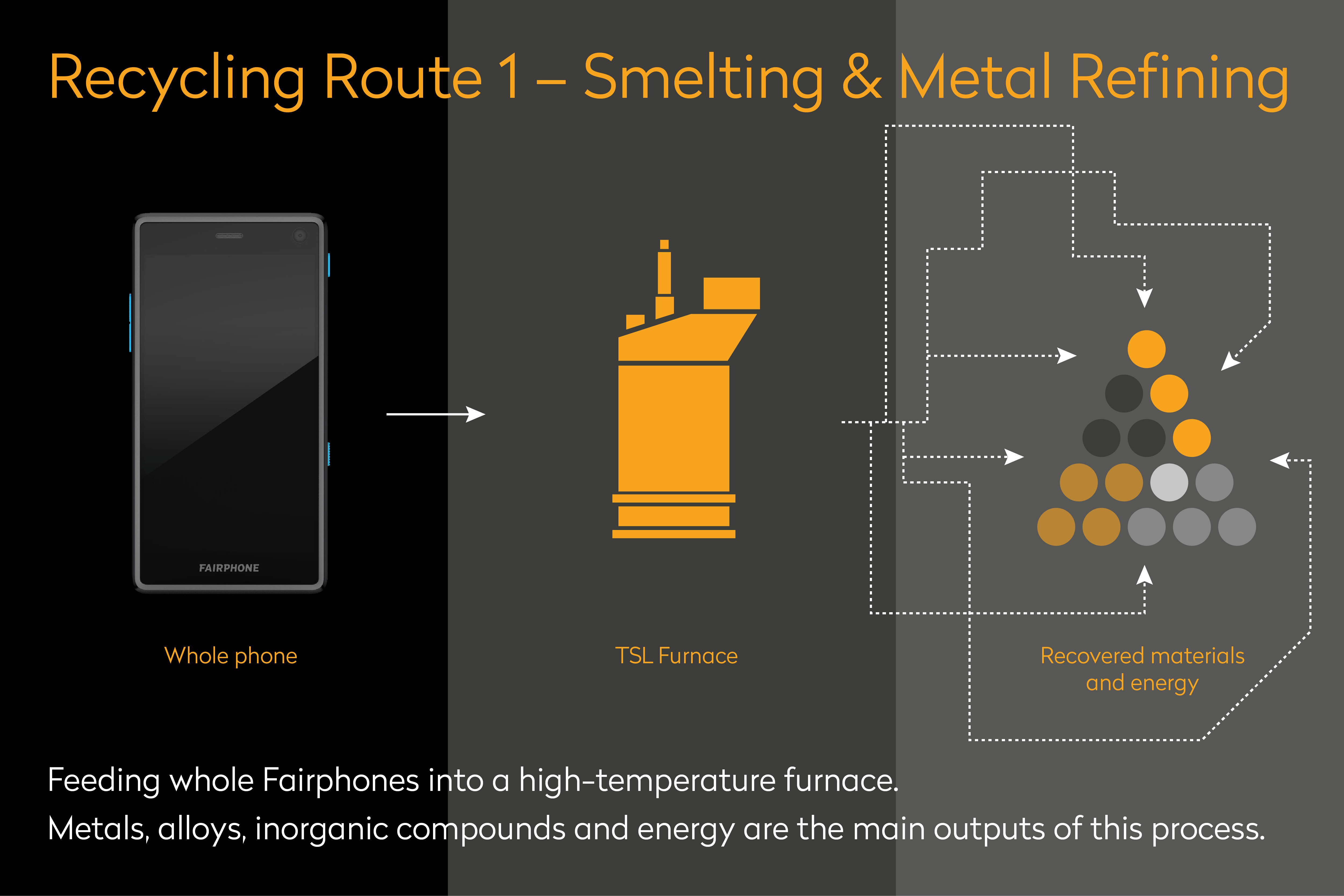
Selective smelting: Separating Fairphone 2 modules and putting them through the most suitable metallurgical and plastic recovery processes. For example:
- Camera, core, top and bottom modules go to top submerged lance (TSL) furnace
- Display module goes to light metal remelt/refine, for optimal recovery of materials such as magnesium
- Battery goes to an electric arc furnace (EAF), for optimal recovery of materials like lithium and cobalt
- Back cover goes to the plastics extruder, for optimal recycling of the polycarbonate (plastic)
.
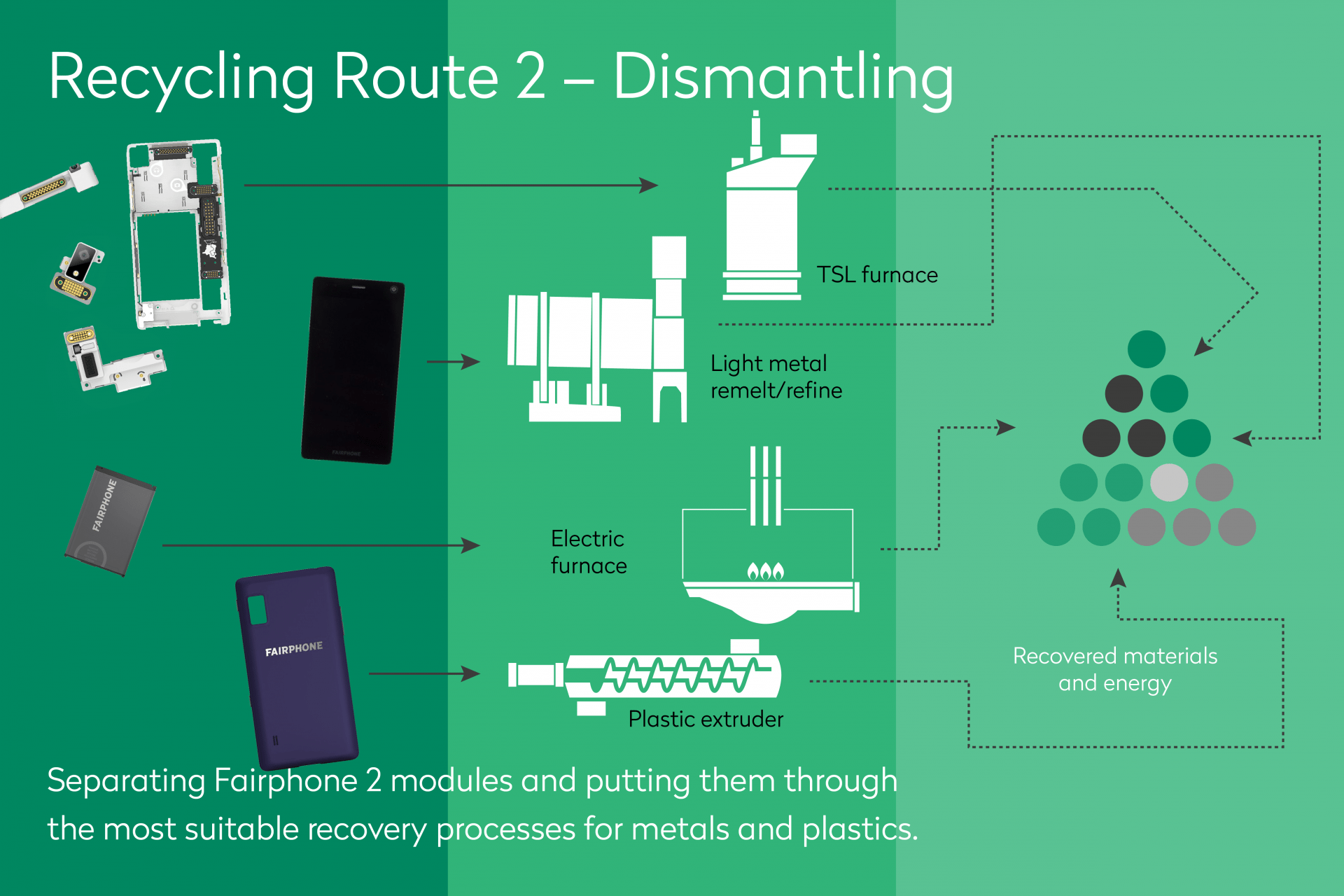
Physical processing and metallurgy: Removing the battery and feeding the rest of the phone through a cutting mill. The resulting scrap is then separated into the relevant processing streams (metallurgy, refining and plastic recovery).
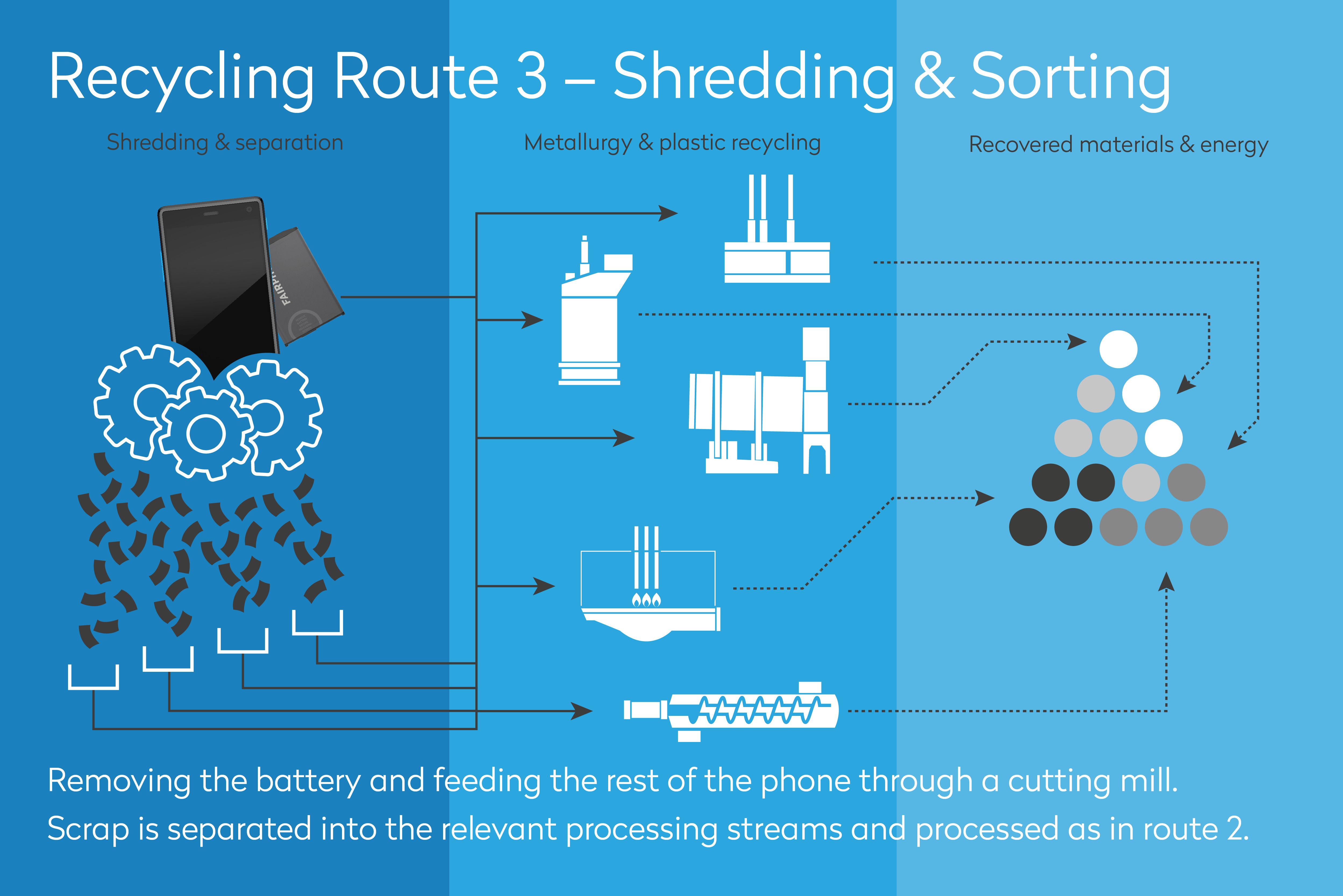
What’s the best-case recycling scenario for the Fairphone 2?
Based on the above descriptions, can you guess which route was the winner?
Well, first the numbers:
Route 1 (smelting) offered the lowest percentage of recovered materials by weight (14% metal recycling, 25% total material recycling and 36% recovery (= recycling + energy recovery) for all materials), as well as a poor range of materials recovered.
Route 2 (dismantling/selective smelting) offered greater recovery of materials by weight (19% metal recycling, 28% total material recycling and 31% recycling/recovery as well as the widest variety of materials recovered.
Route 3 (shredding) offered the highest percentage of materials by weight (22% metal recycling, 30% total material recycling and 31% recycling and recovery), but the variety of materials recovered was more limited than route 2 due to the nexus of creating complex mixtures, dust etc. by shredding/cutting.
As you can see, the answer requires balancing quite a few variables. For example, if you only look at metal recovery, you’ll see it increases significantly from route 1 (lowest) to route 3 (highest). But while route 3 is the best for recovering bulk (non-precious) metals (normally present in large quantities), this method results in impure mixed plastic recyclate which can only partially be reused for consumer products – it’s used mainly as a secondary fuel resource instead.
Therefore, based on the combination of variety of recovered metals and recovered reusable plastics and the effort that has to be put in physical processing, recycling route 2 is the best option for recycling the Fairphone 2. It also comes out on top when you consider environmental impact and energy recovery, which we’ll cover in more detail in the next blog post in this series.
And because this method relies on partially dismantling the Fairphone 2 and its modular components, it offers a strong argument in favor of our modular design approach. In addition, the modular construction improves the recovery of specially valuable minor elements such as gold, rather than just bulk metals.
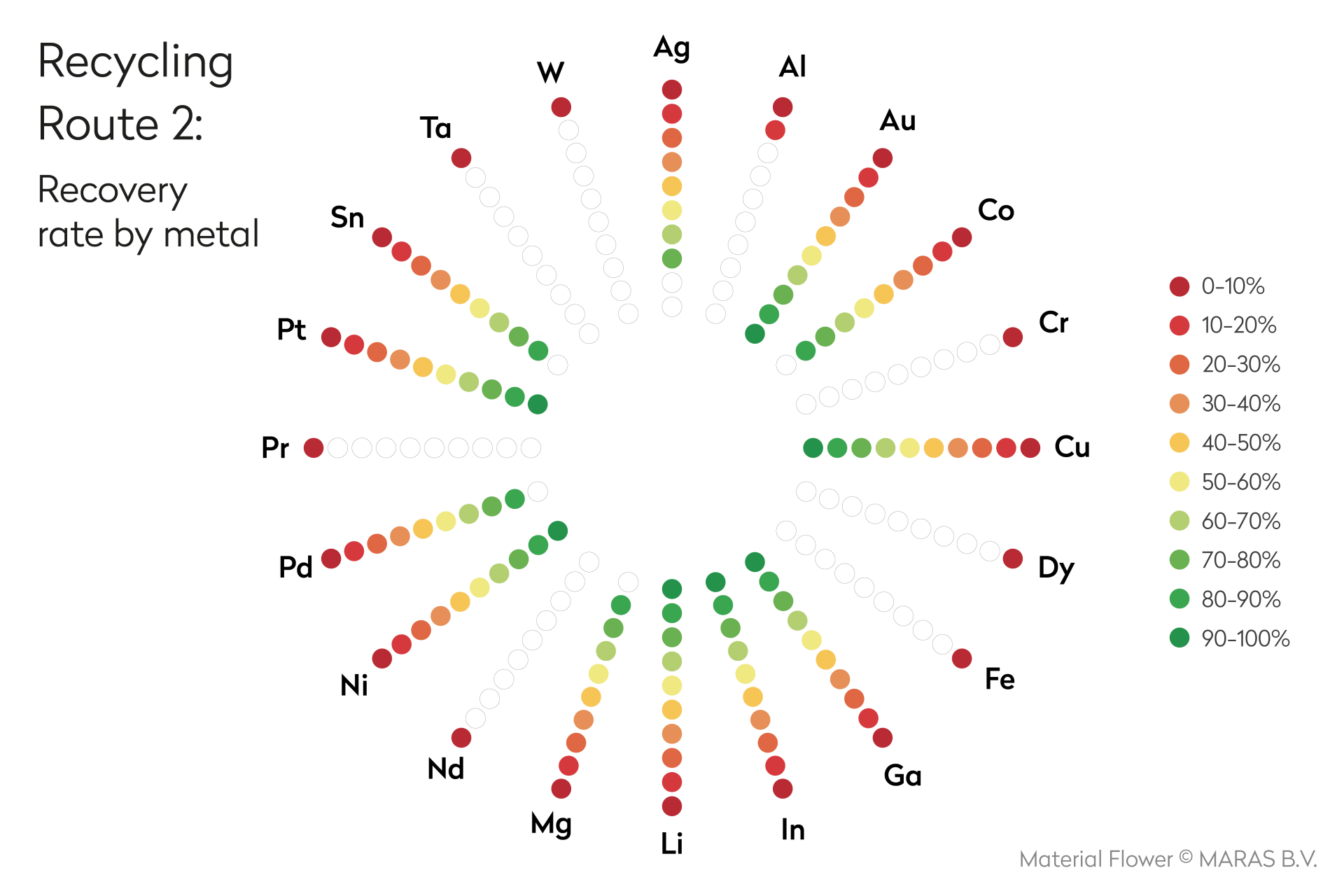
- Materials such as gold, copper, silver, cobalt, nickel, palladium, platinum, gallium, indium and zinc can all be recovered in high percentages (80 to 98%), and modularity promotes their recovery.
- Different recycling routes can result in different recovery rates for certain materials. For example, in route 1, magnesium completely oxidizes in the furnace, meaning a 0% recovery rate. However, using the method in route 3 (where magnesium is liberated and sorted from the other materials into a high quality recyclate), you can recover 92% or 90% with route 2 but with less CO2 emissions.
- Tungsten and tantalum are very difficult to recover unless the parts containing them are removed and processed separately (offering an argument to even extend modularity).
- Plastic recovery depends heavily on how much of the plastic can be separated before the recycling or physical sorting process begins (another advantage of modular design).
So as you can see, whether you look at the high-level recovery rates or individual materials, an easy-to-dismantle device offers a variety of advantages when it comes to recyclability.
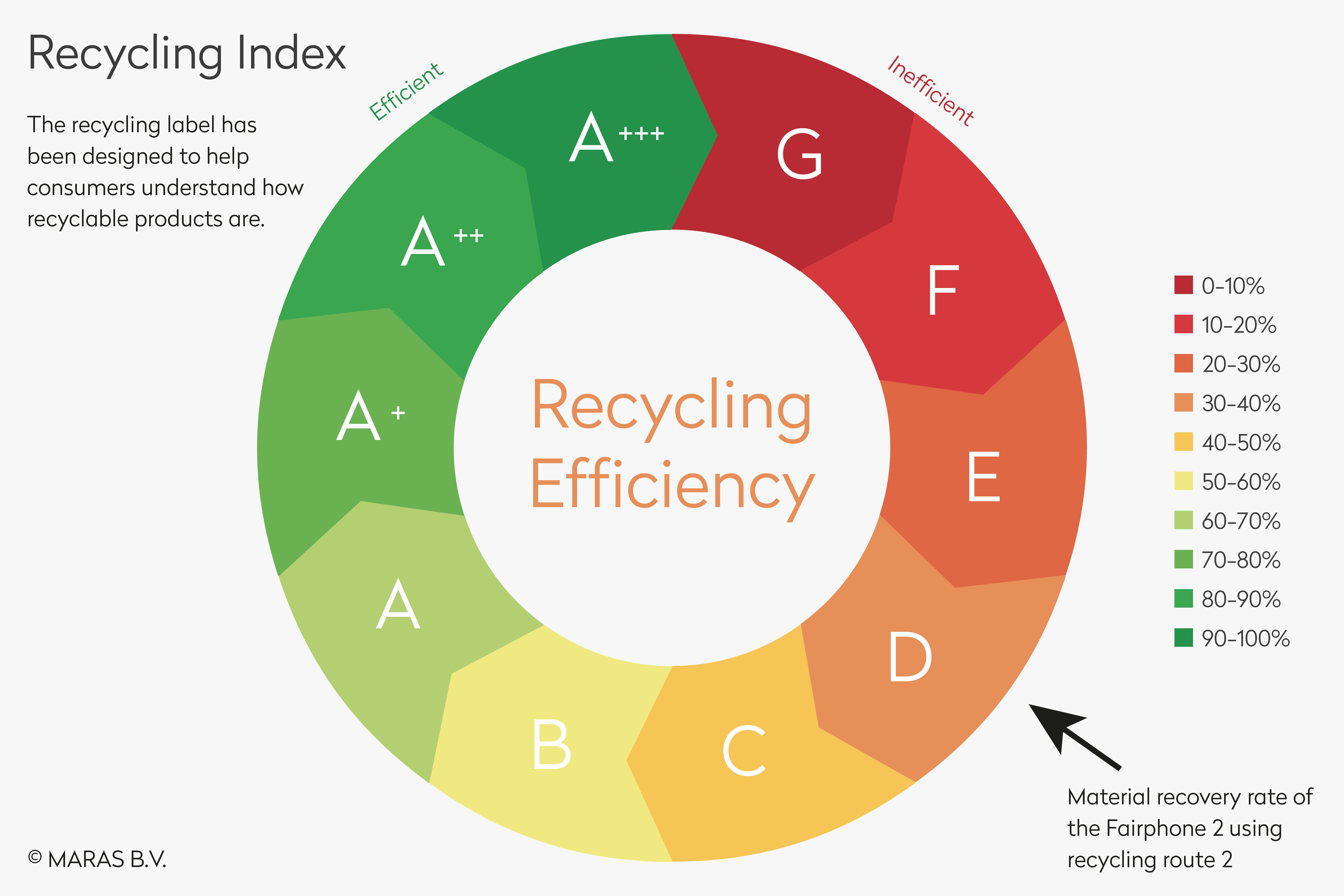
What will we do with these findings?
Combined with the results of mapping our materials and the materials scoping study, this recyclability study gives us unprecedented insight into the materials used in the Fairphone 2 at every stage of their life cycle.
We will use the results of the recyclability study to shape how we manage the end of life of our products. For instance, it will determine the types of recycling partnerships and methods we pursue in the future, favoring an approach that relies on dismantling and direct processing in appropriate metallurgical, energy recovery and plastic processes to maximize material recovery.
This means we need to actively support current activities in the industry that are aimed at finding ways to automate the disassembly of consumer electronics, in order to reduce costs and make this type of recycling more common. In addition, we believe that circular design can advance by taking into account the flexibility to direct material streams to the appropriate processing technologies.
Finally, because the success of different recycling routes is closely tied to the product design, but also to the manufacturing processes and technology inherent to consumer electronics, this study confirms our assumption that modularity can have a direct, positive impact on recyclability. These findings will therefore inform our design decisions for our future products. Our next blog post on this topic will take a closer look at what it means to design for recycling and environmental impact.
Beyond informing our own product lifecycle decisions, we hope that the rest of the industry will benefit from the results of this study and be inspired to gather similar data on a wider range of electronics products. We also hope other players will be encouraged to take a closer look at how product design can impact materials use and recovery, moving us all one step closer to a circular economy.
This study received funding from the European Union’s Horizon 2020 research and innovation programme under grant agreement No 680640.